Our renovation project at Lyndhurst is another good example of commercial work that restores a building’s look and function. We provided the materials, labor, and equipment for the job in the estimate — and even included an addendum to cover window frames and caulking.
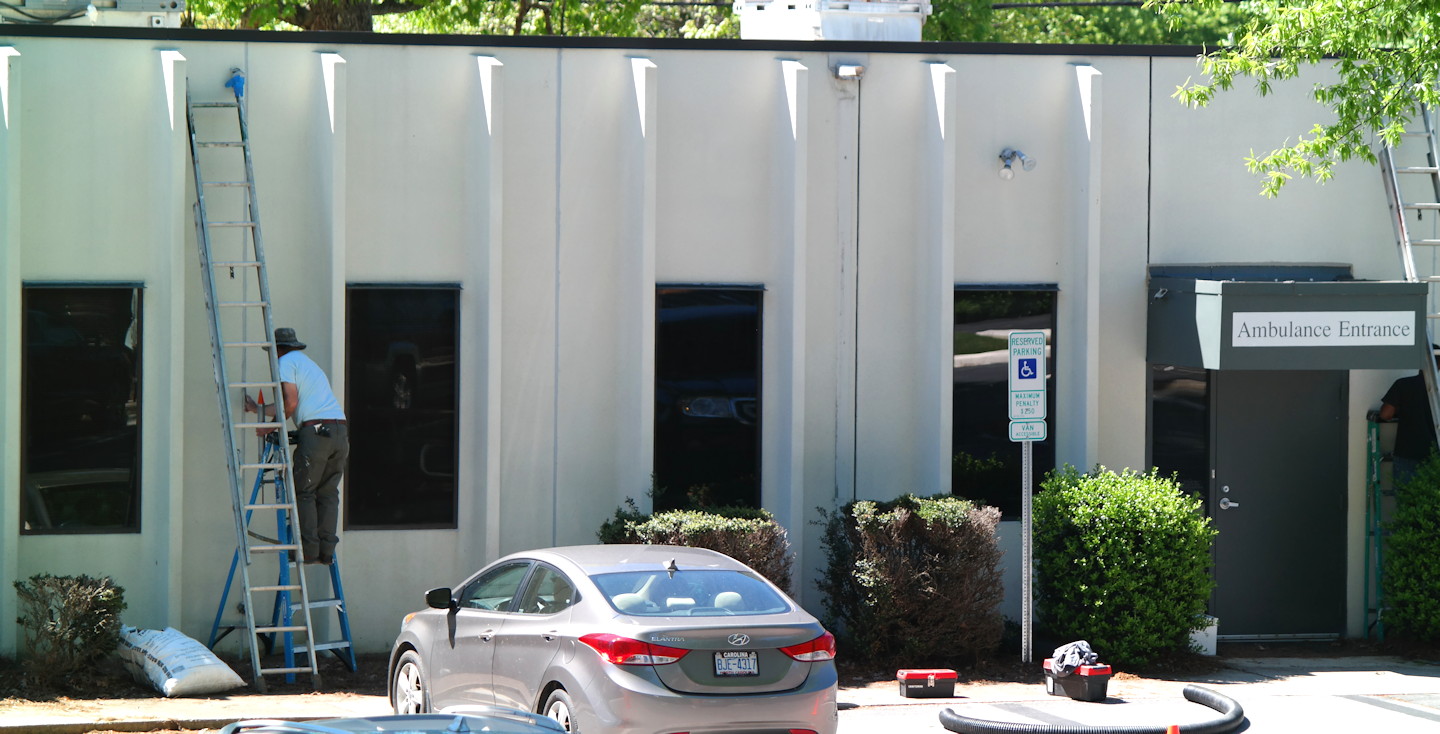
Overview of this Winston Salem renovation project:
- Pressure wash exterior concrete walls to remove residue and contaminants
- Remove the cracked coating on the concrete and prime those areas for new texture coating to blend into existing surfaces
- Pull back the ground around the building to ensure the concrete is sealed to the foundation. Refill the ground areas afterward.
- Remove approximately 1” to 1”1/2 of concrete around the vertical corrugated walls exposed rebar and cracking concrete areas; follow by application coat of “Sika Armatec 110 EpoCem” bonding agent and reinforcement protection.
- Remove approximately 1” to 2” inches of concrete around the top areas of the corrugated walls exposed rebar and cracking concrete; follow by application coat of “Sika Armatec 110 EpoCem” bonding agent and reinforcement protection.
- After bonding agent has been applied to all concrete repaired areas mention above; patch concrete areas with “SikaTop 123 Plus” Two – component, polymer-modified, cementitious, non-sag mortar plus Sika Ferrogard 901 penetrating corrosion inhibitor.
Restoring the proper impression
As a medical facility within a cluster of different offices for Novant, upkeep like this helps retain an image of cleanliness and care. Particularly, as you can see below, in areas where patients enter the building primarily. Teams worked in pairs for safety and attention to detail.
(No one wants to come back to redo a section having missed something small, after all.)
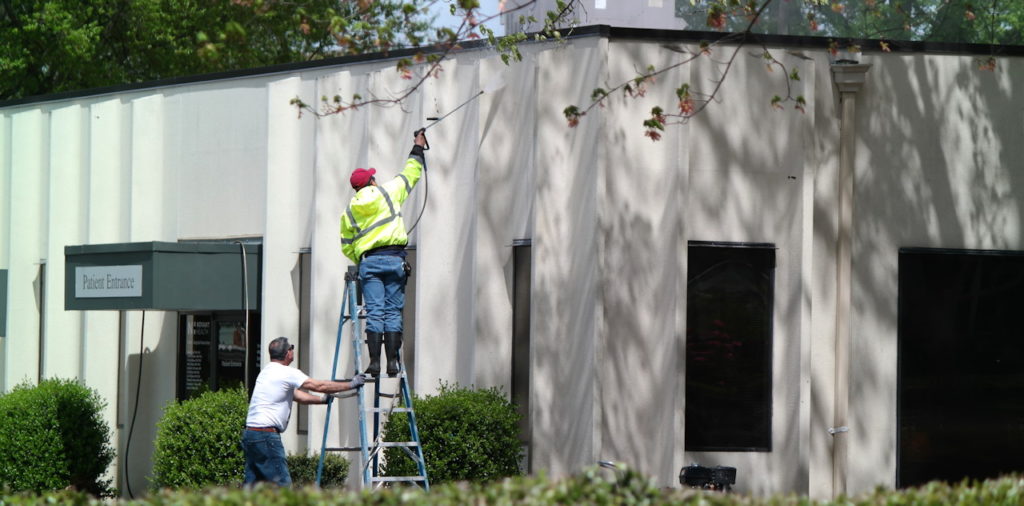
We began the project with a thorough exterior clean to prep the building for the more intensive restoration. This included pressure washing and spot cleans.
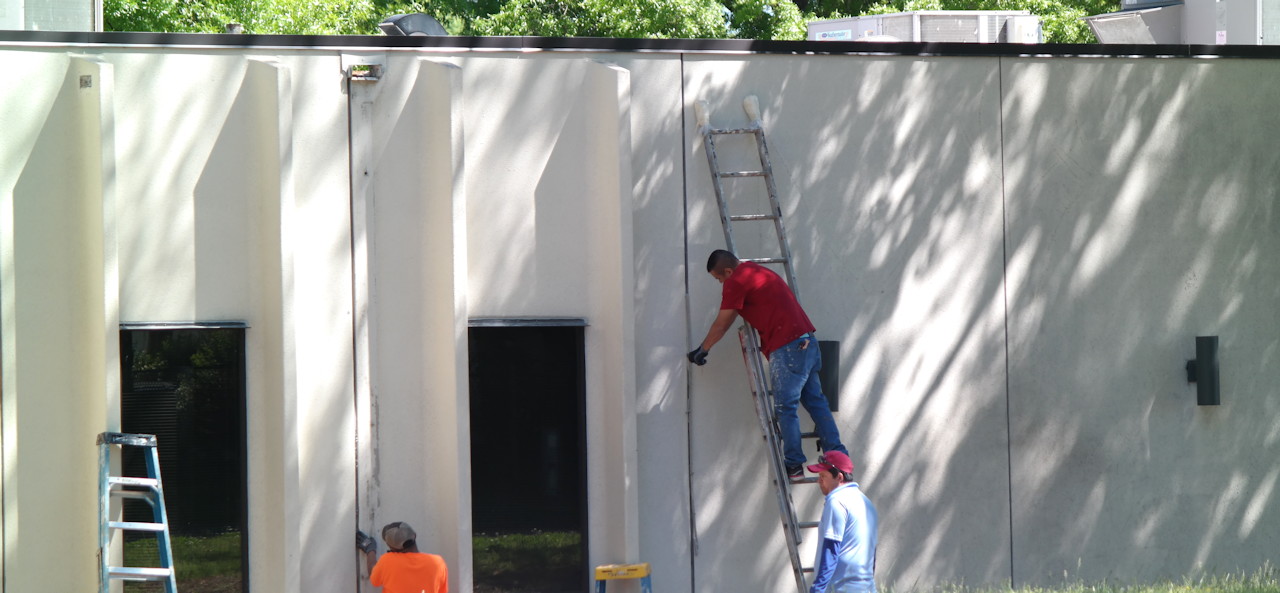
Next up in the building restoration process…
When we stopped by the job site to get these photos the team was in the midst of repainting the building’s exteriors to restore a lustrous white finish.
Teams worked in tandem to complete sections of the building quickly for a consistent look. The weather was cooperative on the day of this shoot, which allowed everyone to work at full speed with no waiting around or prolonged dry times.
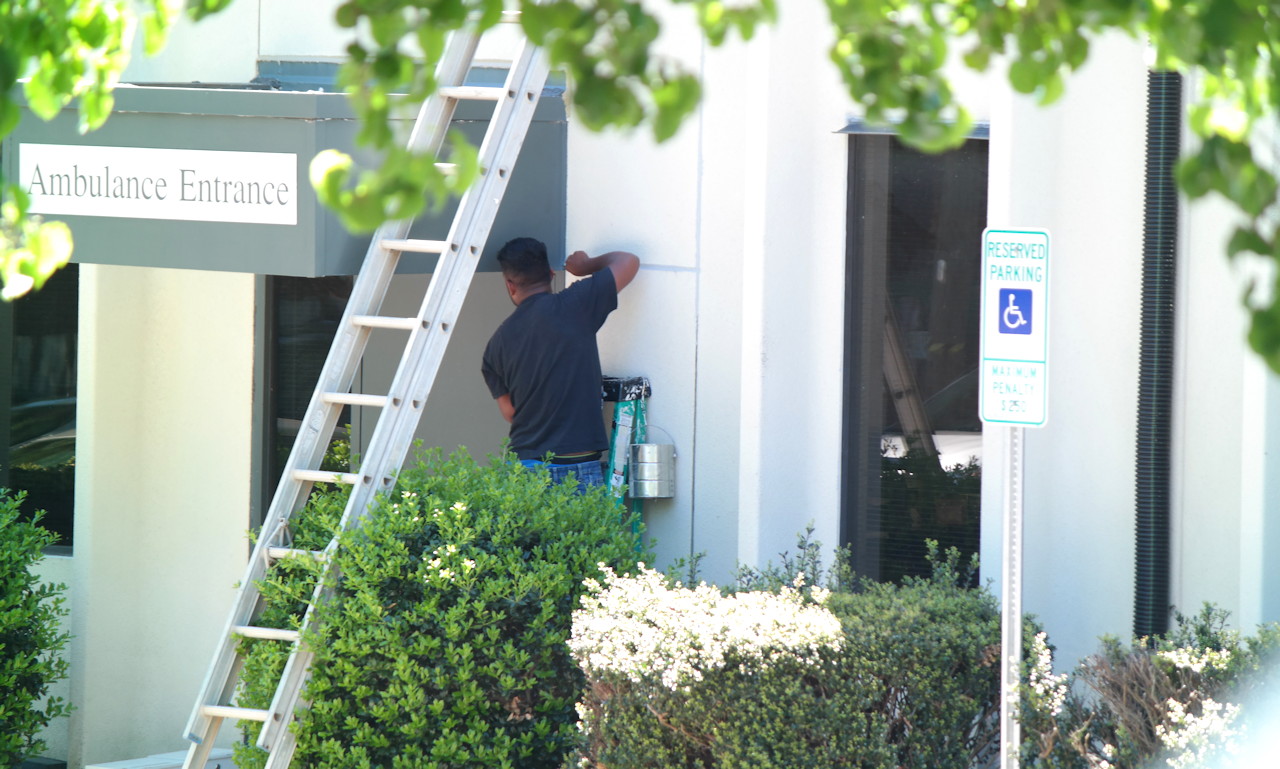
There were certain areas on the outer wall’s ridges where there was visible grime, and also areas where the white paint had worn off over time. As you can see below, this can give a building a dated, weathered look. Luckily the business took action before it became a real eyesore.
However, even this kind of wear can send the wrong message to a first time customer (or the general passerby). We understand that exterior jobs are season dependent and can be an investment when it’s a group of facilities like this one. This is why we work as coordinated and efficient as possible to get you back where you need to be with minimal disruption.
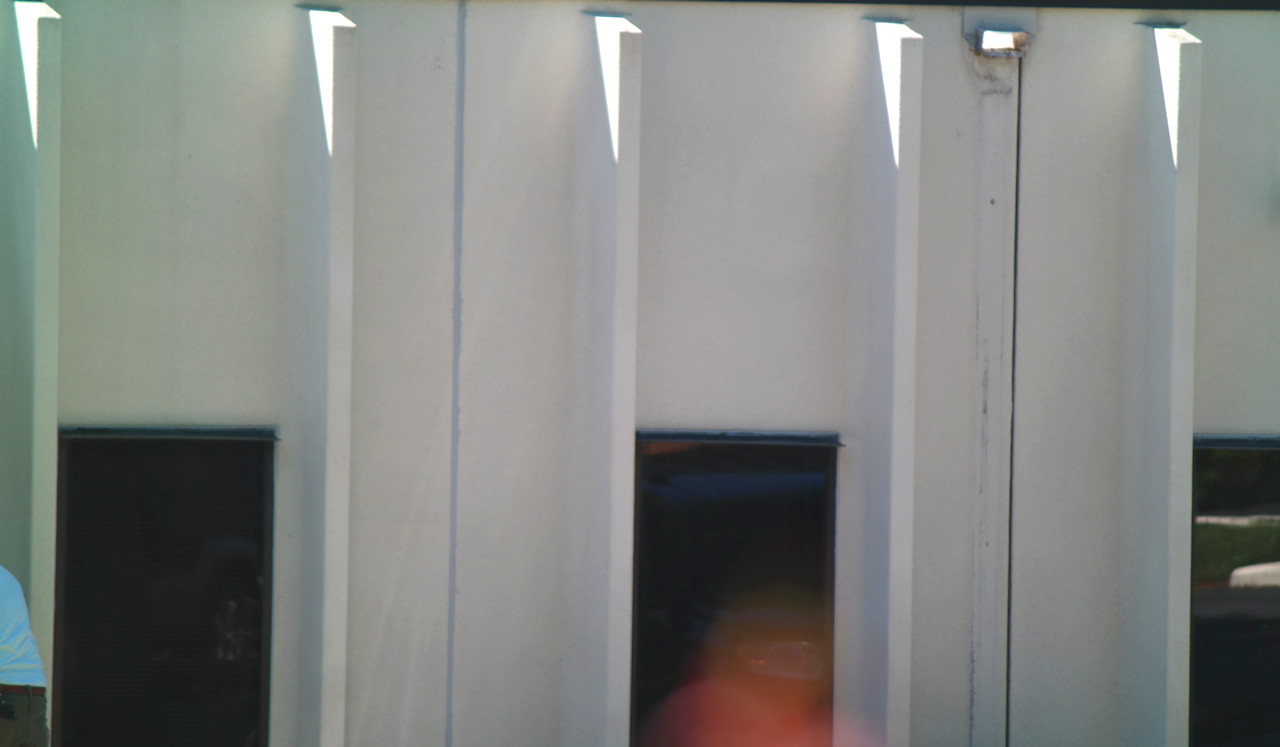
As you can also see in the photo above, the team began sealing the seams with concrete sealant. This keeps moisture out, prevents erosion, and in a more immediate sense preps the surface for a new coat of paint.
The reinforcing agents mentioned in the project spec are a repair measure as well (rather than simply preventative).
As the team applied the new exterior paint, the difference was immediately obvious in the way the fresh luster of the white paint gave the building a “brand new” kind of look. In each place where worn edges and black skids had adorned the surface, there is now only a seamless finish.
If you own a property like this one and have some exterior work to be done, get in touch with us for a quote! This is a good time of year to tackle it before summer is in full swing (and before it’s HOT).